Fukuda Metal's Edge Taper Slit Processing
Edge Taper Slit Processing Let Fukuda Metal handle all your needs when it comes to edge taper slit processing of tab leads.
What Are Tab Leads?
Tab leads are the materials used in the pouch cells found in electric vehicles. Tab leads tend to be thick in order to increase the capacity of the battery for use in cars but the thickness also creates gaps in the welded parts of the sealant film. This can lead to electrolyte leakage.
This is why we developed edge taper slit processing for tab leads. By tapering both edges and welding the sealant film to them, gaps are eliminated and leakage is prevented.
We perform taper processing in addition to slit processing to provide benefits in terms of both quality and cost.
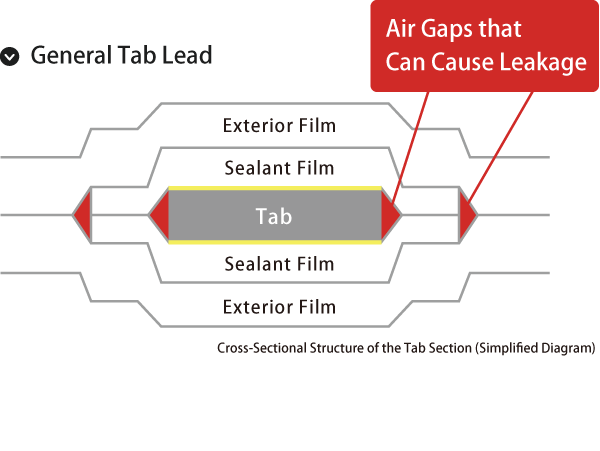

technology Fukuda Metal's Processing Technology
Fukuda Metal's Edge Taper Slit Processing
At Fukuda Metal, we employed a slit processing technique that we developed over many years to create an edge taper slit processing that combines slit and edge tapering. It doesn't require any cleaning or annealing and has fewer steps, creating a superior product to conventional methods in terms of efficiency and cost.
And compared to roll processing, there are no burrs or bulges at the start of the taper so gaps are less likely to form in the welded area between the tab lead and the sealant film, reducing electrolyte leakage concerns.
Conventional Edge Taper Processing
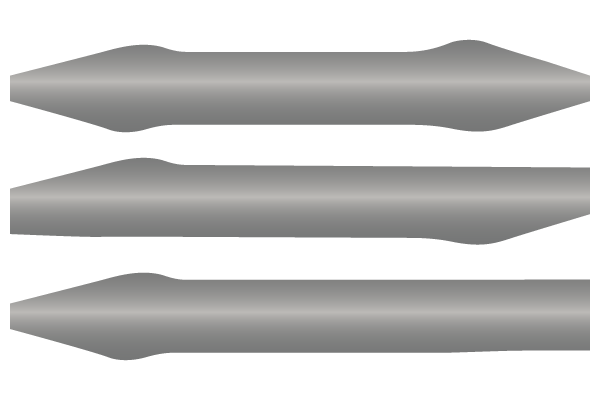
- Variations in all directions
- Thickness isn't uniform
- Bulging occurs at the start of the taper
Fukuda Metal's Edge Taper Slit Processing
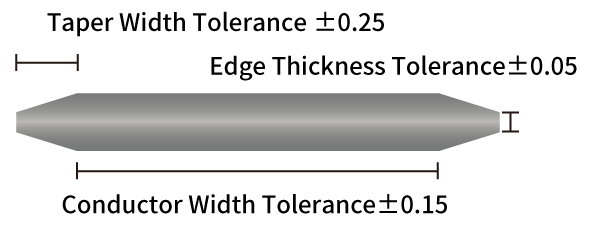
No variations in any direction and a uniform thickness
Comparison with Conventional Processing Methods
Edge Taper Slit Processing | Single-Side Rolling | Full-Surface Rolling | Machining | |
---|---|---|---|---|
Number of Steps | 1Step | 6Steps | 3Steps | 2Steps |
Productivity | ◎ | ○ | △ | △ |
Yield | ○ | △ | △ | ○ |
Cost | ◎ | ○ | △ | △ |
Electrolyte Leak Prevention | ◎ | × | × | × |
Taper Processing Accuracy | ◎ | × | × | ◎※N/A |
Contamination | ◎ | ◎ | ◎ | × |
[One-Side Rolling] Base Material -> Slit -> One-Side Rolling (Edge Taper) 2 - 4 Sides -> Cleaning -> Annealing -> Product
[Full Rolling] Base Material -> Slit -> Rolling (Edge Taper) -> Cleaning -> Annealing -> Product
[Cutting] Base Material -> Cutting -> Cleaning -> Product
[Edge Taper Slit Processing] Base Material -> Slit Edge Taper -> Product
Slit and edge taper processingmakes it 1 step!
Stable Quality
High Mass Productivity
Fast delivery
Cost Reduction
High quality
control
- Compared to Roll Processing There's No Bulging at the Start of the Taper
- Compared to Cut Processing There's No Metal Powder or Other Contamination
quality Fukuda Metal's Quality Control
Quality Policy
With regard to our non-ferrous coil material slit processing, we aim to improve the quality of our goods, services, and operations to ensure the satisfaction of our customers.
We always understand our customers' needs accurately and provide a reliable response. Moreover, we comply with all laws and regulations while being committed to continual improvement.
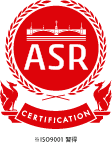
Commitment to Quality
A central focus of our company is setting annual quality-related objectives and working as a team on quality-related equipment, jigs, work environments, and quality control improvement activities.
Management System
The Quality Assurance Department is the heart of our focus on the three key aspects of process management, quality verification, and quality improvement, with an emphasis on establishing work standards, on-the-job training, equipment management, and corrective maintenance.
- Our pursuit of quality starts from the customers' perspective as we strive to ensure quality that instills peace of mind.
- We will continue to gather new information along with our partner companies and with an eye toward the future so we can use the machines and jigs to maintain and improve on our high processing precision.
- We strive to maintain our quality control and quality assurance systems while continuing to engage in quality improvement activities.
Equipment
With regard to equipment, we work with machinery manufacturers to ensure reproducibility as much as possible and stabilize processing quality through mechanical improvements. Regarding jigs, we focus on incorporating feedback from the field and equipment updates to drive our commitment to maintenance and improvement.
Product Inspection Using a Thickness-Curvature Measuring Device and Database Management
After the slitting inspection, the quality inspection which used to be done solely by hand now incorporates a device that measures thickness and curvature for a rigorous inspection process. With this system, we can inspect with an accuracy within a previously impossible 1/1000mm margin of error to deliver higher-quality products to our customers.
[Thickness-Curvature Measuring Device (Made by Keyence)]
We can now inspect to within a 1/1000mm margin of error, something that was previously impossible. It also links to a PC so data can be input directly and easily managed to allow for accurate and timely inspection results.
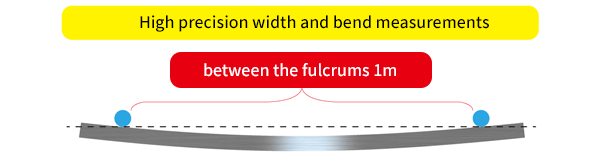
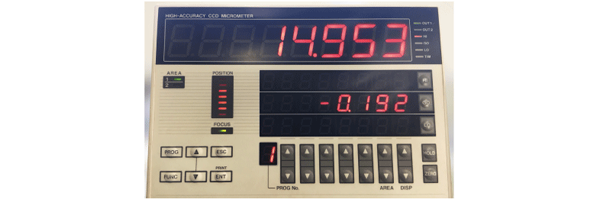
Computer-Integrated Weight and Measurement System
Thanks to the implementation of a weighing system, the issuing of weighing labels, weighing lists, and packing slips for products approved after quality inspection can be done more rigorously and efficiently. Through this system, we can carry out all the work from packing to shipping more accurately and quickly.
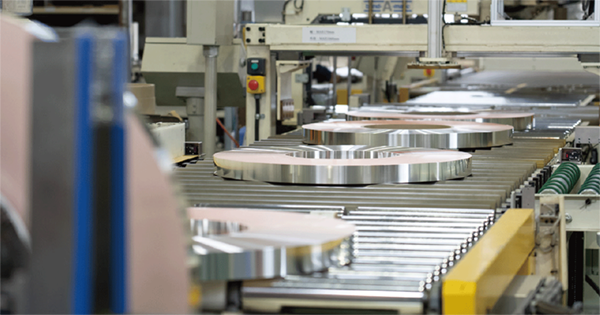
Feel free to start by contacting us
About Fukuda Metal
show site >Company name | Fukuda Metal Co., Ltd. |
---|---|
Representative | Representative Director / Yoshifumi Fukuda |
Location | 〒336-0975 705-1 Daiyama, Midori Ward, Saitama City, Saitama Prefecture |
Establishment | May 10, 1994 |
Founding | June 30, 1994 |
Corresponding bank |
Aoki ShinkinBank Mizuho Bank, Ltd. The Musashino Bank, Ltd. |